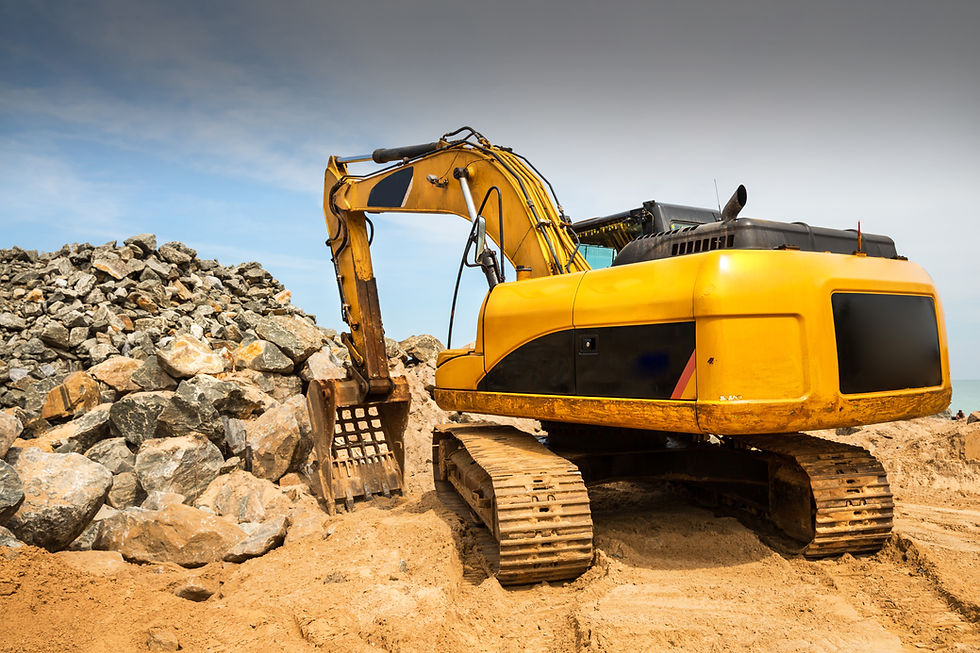
Piling Divisions
and Civil Works
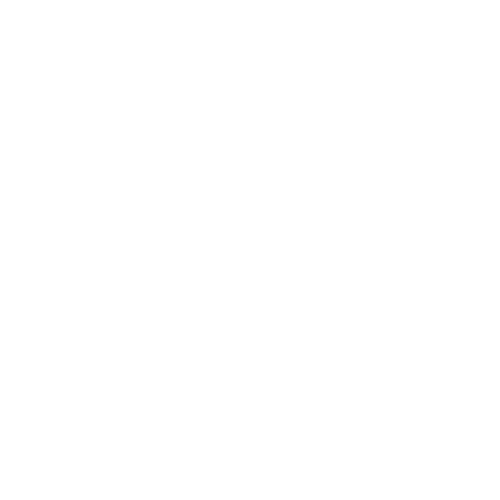
Deep Foundation Pile
Deep Foundation Pile are necessary where the bearing capacity of the surface soils is insufficient to support loads imposed and so they are transferred to deeper layers with higher bearing capacity. Pile foundations are deep foundations. They are formed by long, slender, columnar elements typically made from steel or reinforced concrete, or sometimes timber. A foundation is described as 'piled' when its depth is more than three times its breadth. Pile foundations are principally used to transfer the loads from superstructures, through weak, compressible strata or water onto stronger, more compact, less compressible and stiffer soil or rock at depth, increasing the effective size of a foundation and resisting horizontal loads. They are typically used for large structures, and in situations where soil is not suitable to prevent excessive settlement.
Horizontal Directional Drilling (HDD)
Horizontal Directional Drilling (HDD) is a method of installing underground pipelines, cables and service conduit through trenchless methods. It involves the use of a directional drilling machine, and associated attachments, to accurately drill along the chosen bore path and back ream the required pipe. The first stage consists of drilling a small diameter pilot hole.
Drilling fluid is pumped through the drill pipe to the drill bit where high-pressure jets and the bit will grind the soils ahead of the drill stem. The drilling fluid will also carry the cuttings back to the entrance pit at the drill rig. Tracking of the pilot hole can be done in several ways depending on the size and complexity of the shot. Smaller shots are done using a walkover guidance system whereas the larger more complex shots have a wire line magnetics type system. With both methods there is a transmitter or steering tool located near the drill head which sends a signal to the location engineer giving the exact coordinates of the drill stem. Readings are constantly taken which check the depth, alignment and percent slope of the drill head. Corrections will be made by the operator and locator to keep the pilot hole along the predetermined bore path.
The speed of the pilot hole will vary upon existing soil conditions and the amount of steering which is required. Upon reaching the exit point, the beacon housing and bit is detached and replaced with a reamer. The second step is to pre-ream the pilot hole and enlarge it to a size sufficient to safely install the product lines. A reamer is pulled back and rotated while pumping drilling fluid to cut and remove solids to enlarge the hole. Pre-reaming speeds will vary depending on existing soil conditions and the number of cuttings that are removed from the hole. Bentonite and other additives will be used to ensure a clean and stable hole. Bentonite is used to create a “cake layer” around the outside of the hole during pre-reaming. This will help with the stability of the bore hole and with fluid loss or infiltration. Additives such as polymers are used to help break up the clay soils.
A more evenly mixed drilling fluid will prevent any blockages inside of the bore hole. The final step is the pullback of the pipe within the pre-reamed hole. The drill rod and reamer will be attached to a swivel, which is utilized between the product line and the reamer to prevent any torsional stress from the rotating drill string being transferred to the product pipe. As the product pipe is pulled into the drill hole, drilling fluid is pumped downhole to provide lubrication to the product pipe.
Soldier Pile
A soldier pile is a common retaining wall strategy in which H-shaped steel beams (“piles”) are drilled deep into the earth at regular intervals — usually 2 to 4 metres apart. In between each vertical pile, horizontal supports fill the gap, helping to spread the load. Known as “lagging walls,” these horizontal supports are most often made from precast concrete panels, steel girders or pressure-treated timber.
Contiguous Pile Wall
A series of adjacent piles constructed to form an earth retaining structure as a cantilever or a propped cantilever wall. Contiguous piled walls consist of a row of successive unconnected cast-in-situ concrete piles constructed with small gaps between the adjacent piles, formed using CFA or rotary bored piles (replacement piles techniques). Compared to other lateral soil supporting systems, contiguous pile walls are a more simple and economical supporting system due to reduction in cost and construction period when considering small to medium scale depths of excavations.
Sheet Pile Works
Steel is the most common form of sheet piles as it has good resistance to high driving stresses, excellent water-tightness, and can be increased in length either by welding or bolting. They are connected by interlocking. There are four basic forms of steel and sheet piles:
Normal Sections
These include Larssen and Frodingham sheet piles, which are systems of interlocking steel piles. They have good driving qualities and are designed to provide the good strength for low weight. The interlocking system facilitates easy positioning of the piles (pitching) and driving, as well as providing a close-fitting joint to form an effective water seal. In some cases, a sealant can be brushed into the joints prior to pitching which expands in thickness to form a watertight joint. Larssen sheet piles are stronger and easier to drive because of their uniform section shape. Frodingham sheet piles are usually supplied interlocked in pairs, which makes them easier and quicker to handle and pitch.
Straight Web Sections
These are piles that are interlocked and driven to form cellular cofferdams which may be filled with material such as gravel and small rocks
Box Sections
These are formed by two or more sheet pile sections welded together, and are suitable when heavy loads and high bending moments are anticipated.
Composite Sections
These are commonly used in waterfront protection where large bending moments and heavy axial loads are anticipated. A typical composite pile is a double Frodingham section welded to the flange of a universal I-beam.
Tie Rods & Waling Beams
Tie-rod and strut systems are used to strengthen sheet pile walls or combination walls of all types. These walls may be of port and harbour structures, river revetments, retaining walls, cut-off walls, slope protection, and cofferdams. These anchorage systems however, though serves a common purpose, behaves differently when in use. Tie-rod helps to hold sheet piles from being pushed away by lateral forces from the inside such as loads from infill or embankment. They counter pulling forces and serve as tension members. Waling beams are used in combination with tie bars for anchoring sheet pile walls. They allow to spread the load on sheet pile and to concentrate them onto the tie bars. Waling beams and tie bars therefore form a system with strong compatibility with one another.
Capping Beam
The Capping beam is a steel and concrete beam that ties all the piling together, creates the foundation for the suspended slab and helps to hold the earth and neighbouring houses back. The steel reinforcement bars are placed over the top of the piling cages with legs designed to the engineer’s specs. Once the steel reinforcement is complete the concrete is then sprayed onto it and the capping beam is formed.
Anode & Cathode Protection
Submerged sheet pile walls and tubular support piles can be protected against corrosion by either sacrificial anodes or impressed current cathodic protection. Cathodic protection (CP) design effort begins with a basic decision of whether to use galvanic anodes that operate on the natural potential difference between the anode and the structure, or impressed current anodes with an external power supply that can provide a range of driving voltages.
Fenders & Bollards
Marine Rubber Fenders are critical for the energy absorption of a berthing vessel into the berth structure. A single tanker can be over 500 tons so safe energy absorption in worst case scenarios is paramount. The marine fenders primary job is to protect the berthing structure without damaging the vessel hull for all potential vessel types, sizes and approach scenarios. Marine mooring bollards provide a simple yet efficient method for fulfilling mooring requirements to allow safe securing of vessels next to jetties, wharves, berths and dolphins in ports and harbors.
